FUEL OIL TANKS
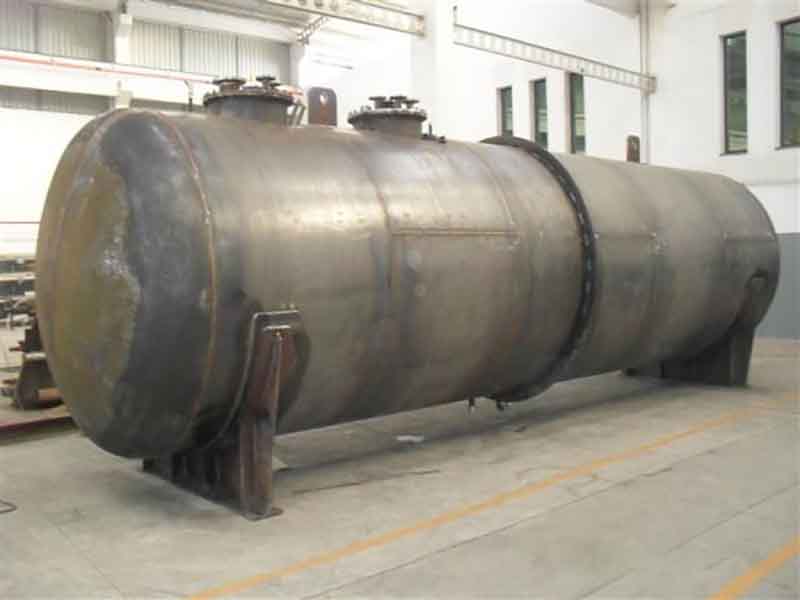
• The fuel tanks are used for storing fuel oil, diesel oil, gasoline and mineral oil.
• Thefuel tanks are construction as single-skin or double skin, according to the demand.
• Double skin fuel tanks are in general provided for underground storage.
• The storage tanks for fuel oil are added with heating unit.
• The tanks are consisted of a cylindrical body and two dished heads. St37 type steel sheeting according to material specifications are used for their construction.
• Welds are made with submerged weld.
• The weld connections are made for nozzles used for filling, discharging, etc. as well as manholes to enter into the tanks.
• Sanding and painting are employed to the tanks, according to their purposes of use.
• Thanks are constructed according to the provisions of TS EN 12285-1, TS EN 12285-2 standards
MULTY-CYCLONES
• They are dry type dust and soot collectors.
• They operate under the principle of centrifugal forces.
• The micro-cyclones are developed to make benefit of high capacity operation, which increases the efficiency.
• These systems are effective for ø10µ and larger particulates.
• The cyclones are provided environment ministry value of emissions as designed according to the capacity requirements.
WET SCRUBBER FILTERS
• Flue gases are wet to move in the water curtain or under the water spraying by nozzles.
• Dust and soot in wet flue gasses have heavier and then leave from flue gasses by crashed to a surface or centrifugal forces.
• White smoke is exit from stack by means of water is vaporized by heating of flue gasses.
• These systems are effective for any size of particulates.
• Some harmful gasses can be kept in flue gasses by means of add some chemical material to the filter water.
• However, since flue gas and filter water mixture acidic medium, the collected wet soot and dust are not neutralized before disposal.
DEGASERS
• The degassers are used to get rid of O2 and CO2 gases contained in the steam boiler feed water in dissolved form to eliminate their adverse effects on the metallic surfaces they contact.
• The gases are separated from the feed water by fracturing the water droplets into tiny particles via sprinkling while they are heated to 102°C and 60°C for O2 and CO2, respectively.
• Degree of pitting induced by the feed water onto pump inlet is directly proportional to its temperature and therefore, the degassing tanks should be installed at high level. This might be accomplished by making use of vertically installed feed water tanks.
• Furthermore, this might also be solved by pressurizing the degassing tanks.
• The degasser heating requirement might partly be satisfied by flushing steam and partly by boiler steam. This may be considered as unwarranted consumption of steam, however, the degassers pay their costs when useful lives of the boiler and installation are taken into considerations.
ECONOMISERS
• Economiser are used for heat recovery from the flue gases.
• Efficiency is depend on where the system is condensing and non-condensing.
• These systems are paid to capital cost in few years. Their operations are free from additional supplementary power.
• Economisers can be fed hot water which plant requirement, without additional hot water boiler.
• Boiler efficiency can be increased when used for heating fed water to boiler
• Particularly economisers are used within solid fuel system can be used for primary and secondary combustion air heating as heat recovery unit which name is recuperator
• Decreasing flue gas temperature by 20°C by heat recovery saves fuel as much as 1%.
• Ecomomisers are manufactured as smoke-tube, finned tube or stainless steel tube design, depending on the system requirements.
JET PULSE FILTER
The principle in jet-pulse filters is to eliminate dust by passing the dusty gas through felt based bag from the outer surface to the inner surface and in the meantime to collect the dust accumulated on the outer surface by dropping to the hopper underneath of the body using compressed air.The dust accumulated in the hopper is taken out of the filter by dust discharge equipments.The dust usable in the production is moved to the system by means of dust transport equipments.
Our company provides you with optimum solutions for your dust problems with its bag filters that are of fully unique design.